Bonding methods
At DATA MODUL, we have state-of-the-art OCA, LOCA, air, gel and hybrid bonding methods in-house, enabling us to offer customized touch display solutions directly from a single source. We select the appropriate bonding method based on your requirements as well as design and environmental conditions and advise you individually. For our bonding solutions, we always use high-quality and qualified materials, as well as state-of-the-art production methods.
Optical bonding versus air bonding
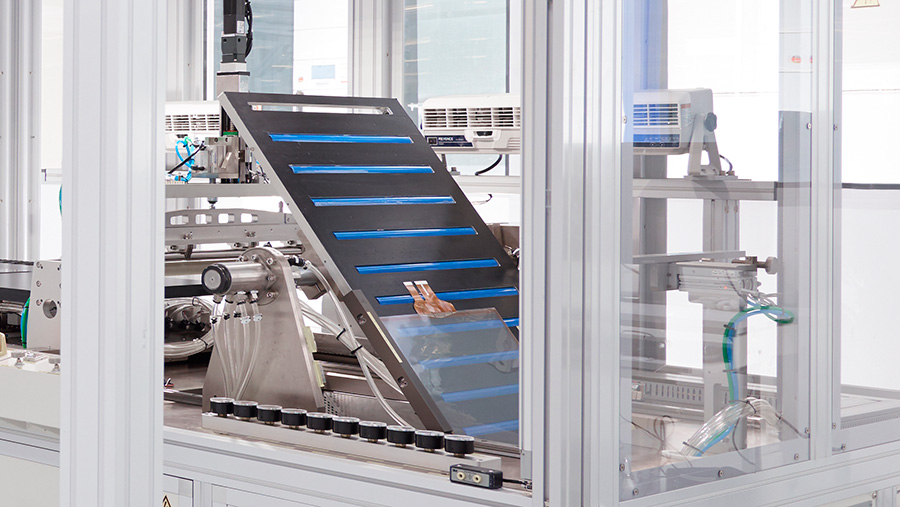
Optical Bonding
Optical bonding enables the connection of touch sensor, cover glass and display into one unit by means of different adhesive technologies. In addition to the classic bonding methods such as OCA (optical clear adhesive) and LOCA (liquid optical clear adhesive), we also offer hybrid bonding. LOCA bonding is suitable for cover glass, SITO touch or display connections, while so-called film bonding (OCA roll lamination) is used to apply the film touch sensor to the cover glass. Hybrid bonding, on the other hand, combines the advantages of the LOCA and OCA processes.
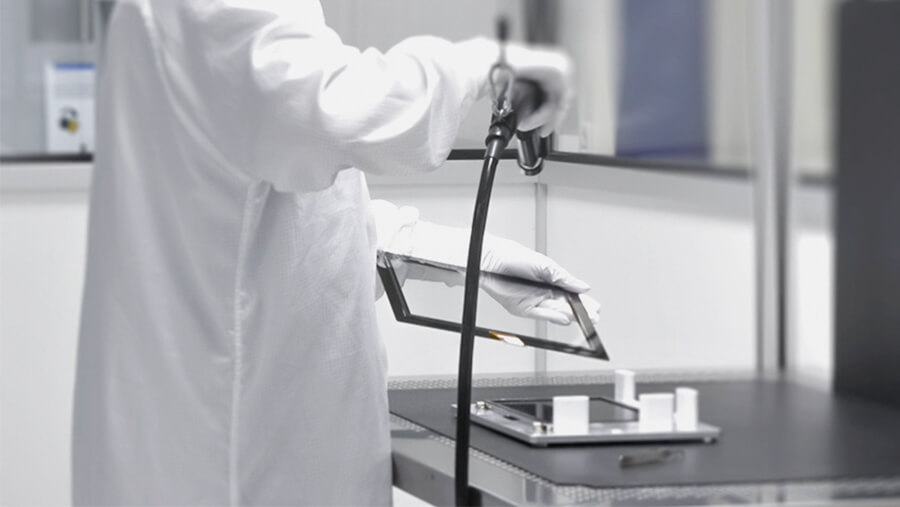
Air bonding
Air bonding is a simple and cost-effective way to connect displays with cover glasses or touch sensors. In contrast to full-surface liquid adhesive bonding (LOCA), air(-gap) bonding involves applying a double-sided adhesive tape all around the TFT frame to bond the TFT and touch glasses together. This cost-optimized process is particularly suitable for indoor applications.
LOCA/OCR bonding
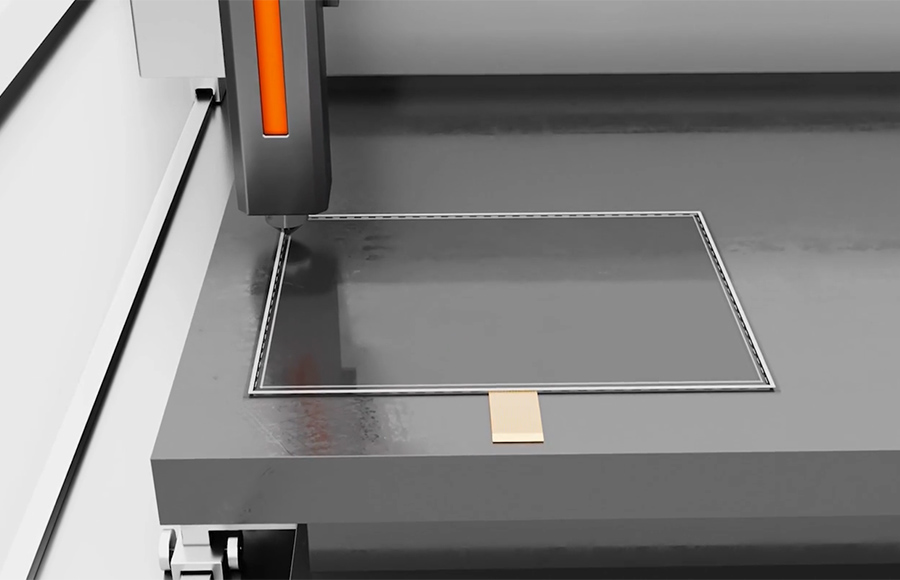
- Hard-to-Hard method
- Flip method (face-down method)
- Liquid adhesive
- Curing by UV light
- Applicable for cover glass, SITO sensors and display
In the LOCA process, liquid adhesive is applied to the cover glass and then the touch/TFT panel is applied. The adhesive spreads evenly and bubble-free between the components. UV light is then used to cure the adhesive without generating high levels of heat, which prevents the material from being stressed by heat or mechanical impact. The LOCA process is one of the most common and established technologies and is particularly suitable for bonding hard materials such as glass, plastic and TFT panels.
OCA bonding
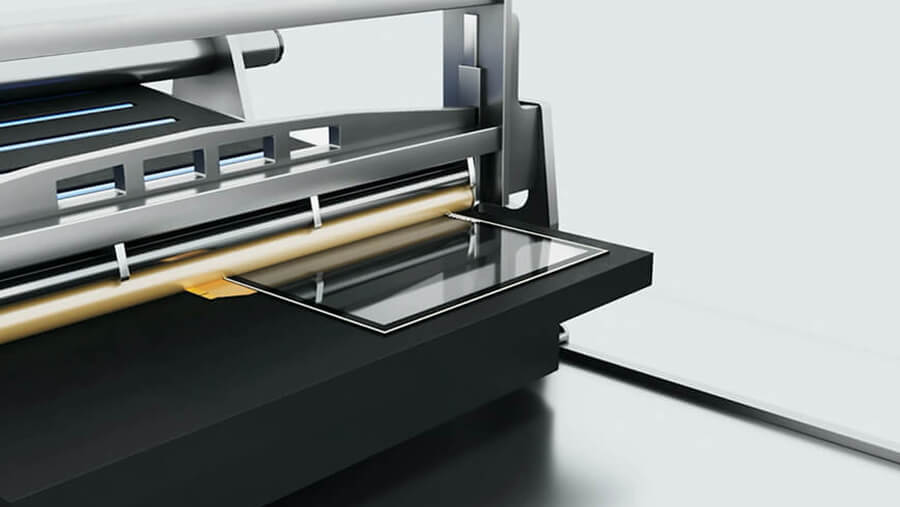
- Soft-to-Hard process
- Free form / curved in planning
- Force-sensitive OCA adhesive
- Curing by autoclave finish process
- Applicable for foil sensors on the cover glass
The OCA process uses an adhesive layer on a touch film carrier to bond the touch sensor to the cover glass using a roll lamination system. Finally, inclusions such as air bubbles are removed with the help of an autoclave. This process can also be used to apply EMC or UV filters and protective films directly to the cover glass or sensor.
Gel bonding
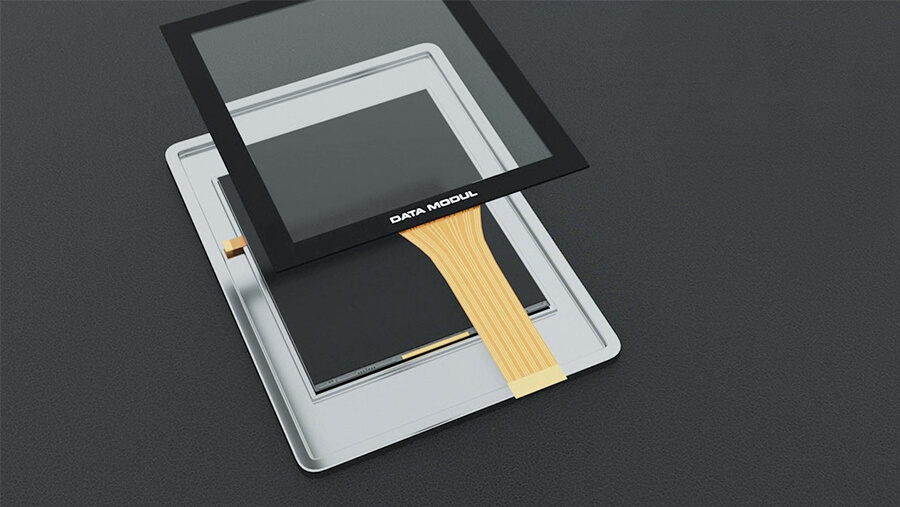
- Hard to Hard process
- Gel pads
- Curing by autoclave process
- Applicable for frameless displays
In gel bonding, the display and touch unit are bonded by means of a gel pad. The width, height and thickness of the pads are cut to fit the size and design of the display. The blank is then applied to the touch unit by roll lamination and bonded to a frameless display. The touch display unit is then joined in an artificially generated vacuum. This process is particularly suitable for bonding displays with thin or no frames.
Hybrid bonding
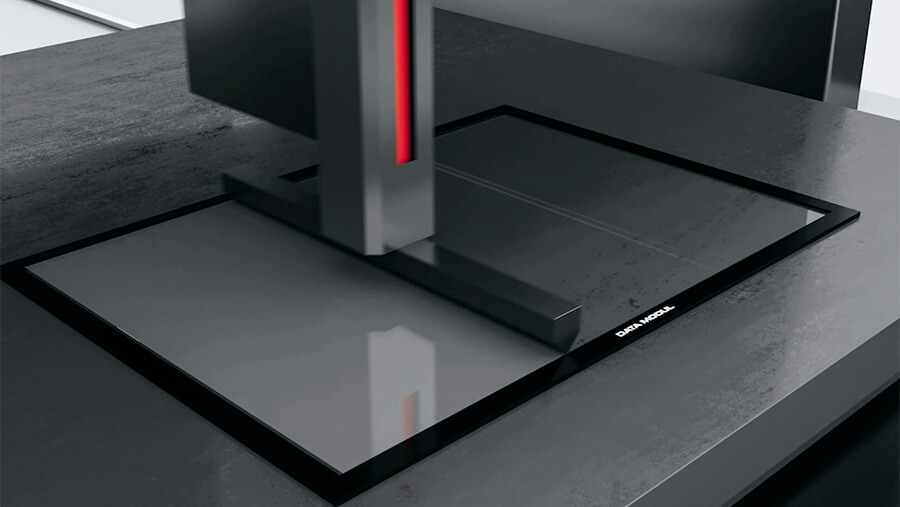
- Hard to Hard process
- Liquid adhesive
- Curing by UV light and vacuum
- Applicable for cover glass, SITO sensors and display for high volume projects
Hybrid bonding is suitable for bonding touch sensors to glass and glass or touch sensors to displays. In this process, liquid adhesive is applied to the surface to be bonded, followed by pre-curing using UV light. The components are then precisely positioned and bonded together in a vacuum, and the adhesive layer is cured with UV light. We have implemented this technology in a fully automated process and efficiently produce touch glass display solutions with high volume requirements.
Pick & place and gap filling procedure
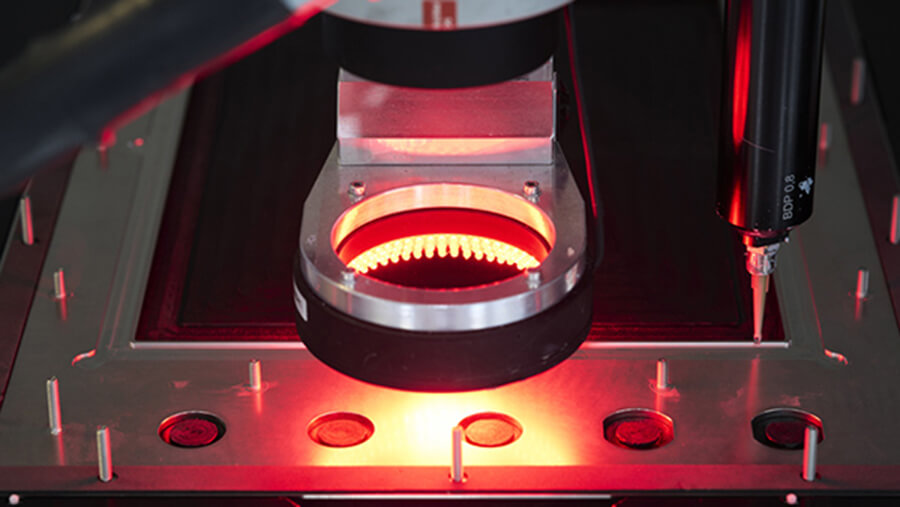
We carry out the bonding of housing components and touch units automatically and under cleanroom conditions. In the process, the components are first measured by a computer to determine the optimum positioning. The frame is then coated with an adhesive and the glass is automatically bonded to the housing part. In the Pick & Place process, a gap is created between the housing and the glass as a result of the process; this is closed in the subsequent gap-filling process by filling an automatically metered adhesive precisely and evenly into the gap. This prevents the possible ingress of contaminants such as bacteria or dirt.